Factory Heating: Hot Well, Hot Water Tank Lining
We were recommended to this client by a major UK industrial boiler manufacturer, as its hot well tank had badly corroded.
The Client
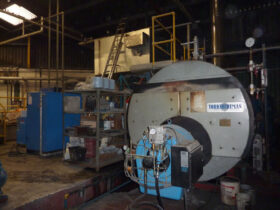
The carbon steel hot water tank was used as part of the factory’s hot water system and also as a steam condensate return tank. It had been recently installed but within six months had suffered extensive corrosion, cratering and pitting below the water line.
Challenges
- Extensive corrosion, cratering and pitting quickly occurred.
- At the current rate of corrosion, replacement or repair was essential.
- The craters and pitting in the steel were 2.5mm – 3mm deep.
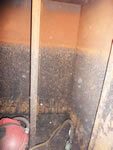
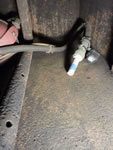
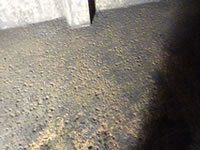
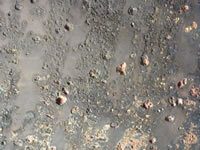
Corrosion in industrial boiler hot well, hot water tank
Solution
Having assessed the rapid wear, we recommended the repair of the tank using a high-temperature resistant tank lining system. We used a high temperature tolerant, solvent-free, glass flake reinforced epoxy resin-based tank lining system. This system, with its cross-linking glass flake reinforcement, imparts outstanding protection to metal and concrete substrates, forming a durable barrier resistant to abrasion, erosion and thermal shock.
All internal surfaces of the tank underwent abrasive grit blasting to SA2.5 and the prepared surfaces were then extensively cleaned using an industrial vacuum cleaner. A high-temperature tolerant epoxy primer coating was initially applied and, due to the deep pitting, it was necessary to apply a resin-based screen over the entire floor and 1m up each wall. Multiple coats of high-temperature-resistant epoxy resin tank coating were applied liberally to achieve a complete and even coverage. On completion, we rigorously tested the treated surface for coating thickness and the absence of micro-porosity in the tank lining. Upon completion of the lining application works and as part of our standard quality control system, we tested for the absence of any holes or micro-porosity in the coating material. This is a safe-to-use, high voltage test designed to detect even the smallest hole in the applied tank lining. Many companies do not carry out micro-porosity checks. We consider it a vital part of our tank lining process and this, together with selecting the best materials for the project, is how we are able to give real-life expectancies for the completed works.
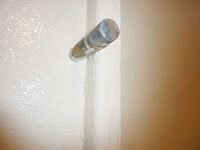
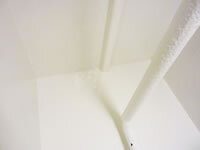
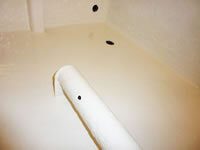
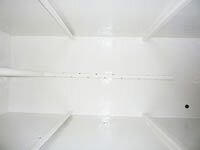
Corrosion in industrial boiler hot well, hot water tank
The Results
This tank lining system will provide outstanding corrosion and chemical resistance. It was specifically designed for use in the most aggressive combinations of high-temperature and chemical environments.
It can be used for potable and non-potable water applications in immersed conditions of up to 125°C and dry conditions up to 200°C. By restoring the tank lining, we were able to avoid the costly replacement of a very young tank, whilst extending its practical working life by an anticipated fifteen-plus years. To avoid any disruption to the site, we were able to work flexibly to complete the work on time and in accordance with our client’s schedule.