Niugini Oil Company, Papua New Guinea: Lining Bulk Fuel Storage Tanks
We were one of many companies contacted by the Niugini Oil Company in Papua New Guinea, which was experiencing problems with their above-ground bulk fuel storage tanks at their tank farm in Lae.
The Client
The tanks, 1,000 tonne Columbia Tec Tanks used to store automotive diesel oil, were weeping between the bolted sections on the joints of the plate overlaps. Rather than replace the tanks, the company was looking for a supplier that could provide an internal lining system that met the American Petroleum Institute API Spec 12B.
We were initially required to treat one tank but following the successful lining of the first tank, we went on to treat seven more tanks for the Niugini Oil Company in Lake.
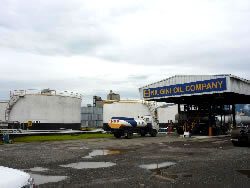
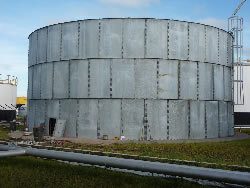
Challenges
- The lining system had to be suitable for application and function under tropical conditions
- Sufficient flexibility to withstand a wide range of temperatures, whilst being chemically resistant to the fuel being stored in the tank.
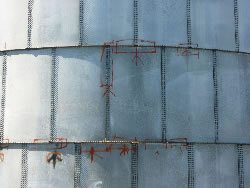
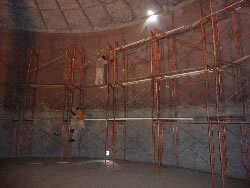
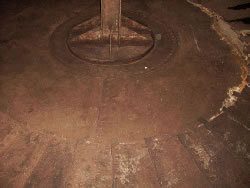
Solution
Having assessed the requirements of the project, we recommended a full internal lining system for the walls and floors, which included the supply of materials and installation.
We proposed a combination of a strong anti-corrosion primer, a special epoxy resin-based flexible jointing compound, followed by two coats of a glass flake reinforced solvent-free flexible epoxy resin tank lining material. To keep costs to a minimum, we advised the Niugini Oil Company to employ local labour for the surface preparation and new lining application works. We provided the materials, application equipment, quality control testing and overall site supervision. All materials and equipment were shipped out by ocean freight and two technical engineers were flown from the UK.
Our engineers confirmed the initial assessment and oversaw the surface preparation, application and testing of the lining system. Having applied multiple coats of a specialist flexible glass flake reinforced epoxy tank lining system, we fully tested the overall DFT and absence of micro-porosity. The tanks were then filled with fuel and further tested to confirm the integrity of our newly applied tank lining system.
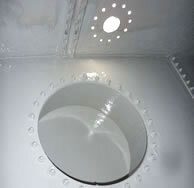
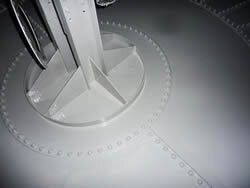
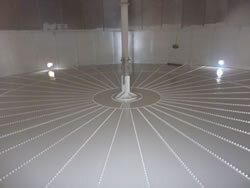
The Results
Despite working in tropical working temperatures, we were able to successfully complete this project on time. Our client was highly satisfied with the finished results. The work on seven tanks was completed over a period of two years and four separate site visits.
Our technology has enabled the Niugini Oil Company to utilise much-needed additional storage capacity at very little cost. An additional advantage of our system is that the tanks can be easily maintained and cleaned, mitigating any risk of product contamination.