Tank Lining
In over 35 years of working with tanks, we have found that almost any tank, in any condition, can be lined up and brought back into service.
- Cost on average approximately 10% of the cost of replacing a tank
- Lining Installation work on large tanks completed in a few short weeks.
- Lining installation work on small tanks completed in a few days.
- Can extend the practical working life of a tank by 30 plus years. (2)
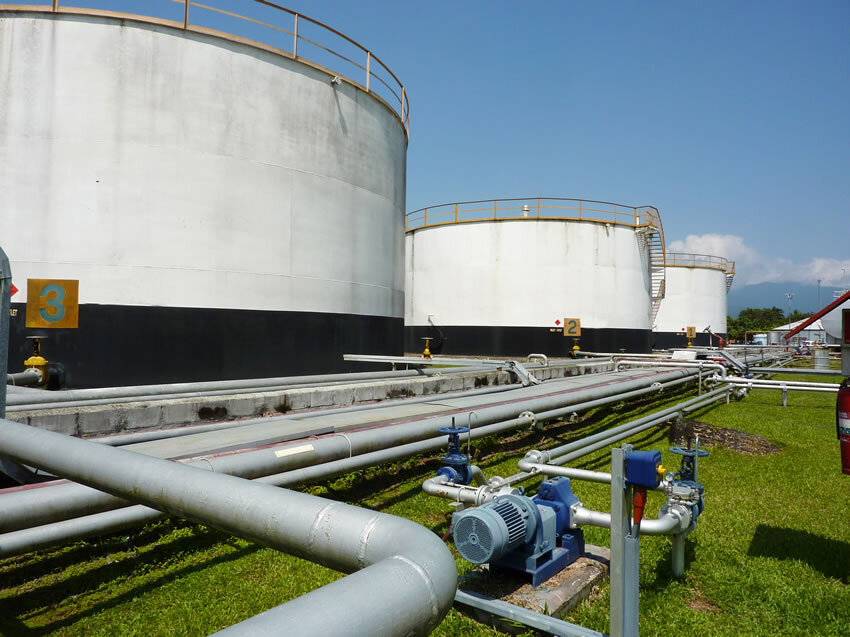
In our throwaway society far too often, older tanks are discarded when in reality they can deliver effective service for many years to come.
We have revitalised many tanks which would have otherwise been dismantled and destroyed needlessly, with all the cost, hassle and financial implications of removing the old tank and installing the new one.
At Specialist Coatings we repair and restore old corroded tanks with our solvent free technology, to further the life of the tanks by 5 to 25 + years depending on the system used and our customer’s requirements.
In our many years of experience we have refurbished tanks in every conceivable condition of corrosion and decay with many problems, but we always work with the customer to find the most cost effective solution.
We pride ourselves on our longevity within the industry, and our commitment to restoring corroded and neglected tanks nationally and internationally.
Specialist Industrial Coating Systems Ltd carry out surface preparation, application and testing an extensive range of tank lining products which are designed to meet every corrosion and containment challenge. The refurbishment or lining of an existing tank is more cost effective than replacing a tank and certainly more environmentally friendly.
A minute hole in the internal protective lining of an aggressive chemical bulk storage tank can rapidly become an extremely serious problem. It is potentially very dangerous to personnel and the environment and could lead to product loss and wastage.
Any contamination of food or drink stored in a process vessel with a substandard internal surface could necessitate the disposal of the entire production batch or permanently give your client a lower impression of the standard of your product than it really deserves.
The cost of a failed container is not only the repair cost, but the lost material or product, the lost time and in some cases the cost of providing a replacement tank.
The rules that we apply have been learned from many years of experience:
- Choose the right materials for the job
- Prepare the surfaces correctly
- Apply the coating as specified
- Test the results
There are no short cuts: to stop corrosion and to protect the tank we use the right materials, the right tools for the job, and we test the results until we are completely satisfied.
In short… We are specialists.
All our services are available as a single turn key operation or on a consultancy basis for any element from specifying a suitable lining material, preparing and applying the new lining, to quality control, inspection and testing the work by other contractors. (including dry film thickness and micro-porosity checks.)
Food grade, chemical resistant and high temperature lining material variants available.
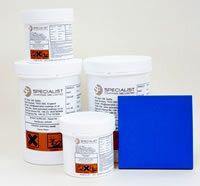
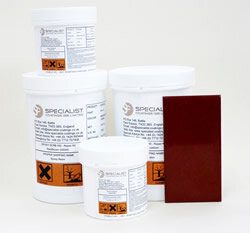
For lining tanks and vessels made from
- Concrete
- Fibreglass
- Stainless Steel
- Steel, Mild or Carbon
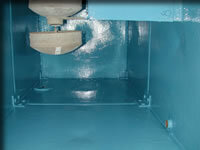
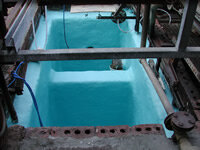
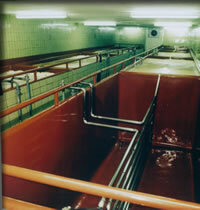
Areas for use
- Braithwaite Panel Tanks
- Chemical Tanks (including acids, alkalines and solvents etc)
- Corrosion Prevention
- Environmental Protection
- Erosion Prevention
- Food & Beverage Tanks
- Fuel Tanks
- Plenums and other Air Chambers
- Steam Condensate Return Tanks
- Tanks in Confined Spaces
- Water Tanks
- Waste Water Treatment Plants

Lining Materials Frequently Used
- Epoxy Resins
- Fibreglass Systems & Resins
- Glass Flake Reinforced Resins
- MIO Materials
- Polyurethane Resins
- Polyurea Resins
- Solvent Free & Solvated Resins
- Vinyl Ester Resins
- Water Based Resin
In this Section
- 1Tank Linings
- 2Bund Lining
- 3Water Tank Lining & Tank Joint Repairs
- 4Fiberglass Tanks
- 5Brewery, Winery, Distillery and Food Industry Tanks
- 6Conrete Tanks & Chambers
- 7Hot Water Tanks
- 8Heat & Power
- 9Commercial & Industrial Tank Lining
- 10Marine & Maritime
- 11Narrowboats, Barges, Wide-beams, Canal Boats, Houseboats, Leisure Cruisers & General Water Craft
- 12Steel Tanks
- 13Food & Drink